July 23, 2025
Rubber molding is gaining traction across the manufacturing landscape, and for good reason. As industries face increased pressure to deliver cost-effective, durable, and sustainable products, rubber molding has emerged as a reliable solution. Its ability to meet demanding performance specifications makes it especially valuable to industrial manufacturers seeking to streamline production. Whether you’re fabricating parts for the abrasives, metal finishing, or general industrial sector, rubber molding offers the adaptability and efficiency required to stay competitive.
Rubber molding is useful for companies dealing with surface treatment equipment, machinery handling, and friction-intensive applications. In sectors where precision and reliability are non-negotiable, molded rubber parts are often used to protect components, absorb shock, or ensure secure contact between materials. These features contribute to smoother workflows and reduced mechanical failures.
The versatility of rubber also allows it to serve as a barrier or insulation layer in many industrial assemblies. In settings where vibration, heat, or contaminants can disrupt processes, molded rubber parts provide a dependable buffer. These characteristics extend the life of nearby machines and improve overall safety and efficiency. The benefits of rubber molding translate directly to lower maintenance requirements and reduced downtime.
Rubber molding also supports rapid production transitions. When product designs or tooling needs change, mold adjustments can be made relatively quickly, ensuring that the production line experiences minimal interruption. This kind of flexibility is vital in a dynamic market where speed-to-market plays a critical role in profitability.
1. Prioritize Cost Efficiency in Manufacturing
Cost control is a key objective for industrial manufacturers. Rubber molding enables material savings by minimizing waste during production. Techniques like compression and transfer molding ensure efficient material use, allowing manufacturers to cut costs.
Rubber molding typically operates at lower temperatures than many metal or plastic processes, leading to reduced energy consumption and utility expenses. Automation and streamlined workflows also contribute to faster cycle times and lower labor demands.
For manufacturers managing both short and long production runs, rubber molding provides a scalable and cost-efficient approach. Whether fulfilling custom orders or mass-producing standard parts, companies can achieve consistent quality while keeping expenses in check.
Another advantage comes from the reusability of many rubber molds. Once a mold is created, it can be used for repeated production cycles, offering strong long-term ROI.
Another financial benefit is that companies can better predict production costs over time, making long-term budgeting and planning more reliable.
2. Improve Product Durability for Industrial Use
Durability is essential in industrial environments where products must withstand abrasion, vibration, and chemical exposure. Rubber molding delivers components with enhanced tensile strength, flexibility, and resistance to wear and tear.
Components such as contact wheels and rubber rollers endure heavy-duty use across polishing and finishing processes. Rubber's resilience makes it an ideal material for such applications, extending product lifespan and reducing equipment downtime.
Consistent molding techniques also ensure uniform part geometry, which improves functionality and compatibility with other systems. This precision helps maintain reliability across every production cycle.
Rubber molding’s resistance to moisture, UV rays, and chemicals allows these parts to thrive in both indoor and outdoor settings.
3. Leverage Flexibility for Custom Solutions
Rubber molding offers a high degree of design flexibility, allowing manufacturers to produce parts with tailored shapes and dimensions. This is particularly beneficial for companies with specialized machinery or unique process requirements.
Custom-molded rubber components can be engineered to meet specific operational needs, such as vibration isolation or torque transfer. Mold creation services support a wide range of specifications.
With flexible production quantities, manufacturers can test custom designs or scale production as needed. This responsiveness is essential for meeting evolving industry demands.
Rubber molding also supports various surface finishes, which can enhance product performance or presentation.
4. Adopt Environmentally Responsible Practices
Industrial manufacturers are increasingly focused on sustainability. Rubber molding contributes to environmental responsibility by producing minimal scrap and using materials that can often be reclaimed or recycled.
The molding process's low energy requirements help reduce carbon emissions. Producing long-lasting rubber components also reduces the need for frequent replacement, minimizing material waste.
Efficient production with minimal environmental impact supports long-term sustainability targets, all while maintaining high performance.
Incorporating sustainability into manufacturing isn't just about compliance. It also appeals to customers who value environmentally conscious practices.
5. Embrace Proven Manufacturing Technology
While some advanced technologies are still emerging in other sectors, rubber molding continues to deliver value through time-tested techniques. Compression, transfer, and injection molding methods are well-established and dependable.
Modern rubber molding equipment allows for precise control over pressure, temperature, and cycle time. These refinements enable consistent quality and repeatability for industrial-scale operations.
Automation in the molding process improves throughput and accuracy, making it easier for manufacturers to meet deadlines and maintain production efficiency.
With decades of refinement behind it, this method provides predictable results for mission-critical applications.
6. Meet the Demands of Industrial Sectors
Rubber molding supports a wide range of sectors, from metal finishing and abrasives to general manufacturing. Components like contact wheels and rubber-coated rollers play a critical role in grinding and material handling.
The reliability of molded rubber parts ensures optimal equipment performance in high-friction environments. Whether it’s a wheel used in grinding or a molded roller for a conveyor system, rubber components enhance operational stability.
Industrial manufacturers benefit from rubber molding’s adaptability across different processes and operating conditions.
This broad applicability simplifies procurement. Instead of sourcing multiple materials or parts, rubber molding allows companies to fulfill a variety of needs with a single method.
7. Scale Production Without Compromising Quality
Rubber molding is well-suited for both low-volume specialty parts and high-volume production runs. Manufacturers can scale up without compromising on quality, thanks to consistent mold performance and process controls.
Flexible production volumes allow companies to adjust order sizes as needed. This scalability helps manufacturers respond quickly to market shifts or urgent demands.
With rapid quote turnarounds, companies can move from design to production efficiently, reducing lead times and boosting responsiveness.
Rubber molding’s consistency reduces the risk of defects and rework, supporting strong output levels and client satisfaction.
8. Position Your Business for Long-Term Growth
According to Global Market Insights, the rubber molding market size was valued at $38 billion in 2023. This growth reflects increasing demand for rubber components across industrial applications. This momentum signals strong opportunities for manufacturers to expand their offerings and capture greater market share.
Investing in rubber molding helps companies modernize operations while maintaining the reliability and consistency industrial environments require. Whether improving systems or launching new product lines, rubber molding provides a strong foundation for long-term growth.
Its ability to deliver durable, custom-engineered components positions rubber molding as a key resource in manufacturing, especially for those focused on sustainable and cost-effective production.
Rubber molding continues to shape industrial manufacturing by offering durability, design flexibility, and efficient production methods. Its relevance in sectors like abrasives, metal finishing, and general industrial work makes it an essential tool for manufacturers focused on performance.
Contact Rubber Corporation is proud to support
industrial manufacturers across North America and beyond. From custom-molded products to expander and contact wheel recovery, our team delivers high-quality rubber solutions tailored to your needs. We offer precision rubber manufacturing, contact wheel recovery, expander wheel recovery, custom-molded products, and more.
With a 40,000-square-foot facility, global shipping capabilities, QS-compliant processes, and rapid quote turnaround in two–three business days, we’re ready to support your next project. Let’s build better solutions together. Contact Rubber Corporation today.
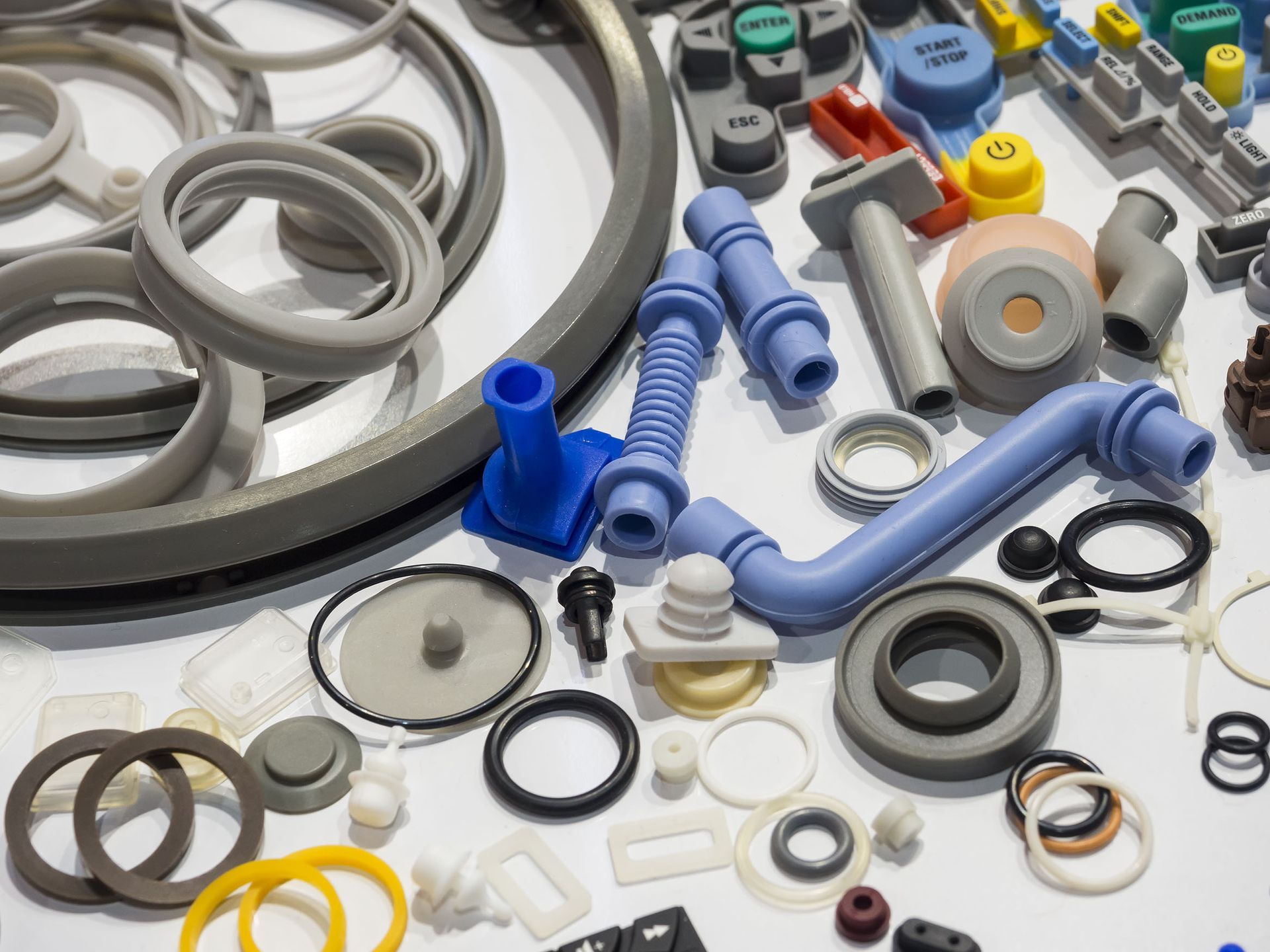